What is mineral insulated cable?
Mineral insulated cable is a kind of cable with copper sheath wrapped copper conductor core, and magnesium oxide powder as inorganic insulating material to separate the conductor and sheath, the outermost layer can be selected according to the need for appropriate protective sleeve. Generally known as MICC or MI cable.
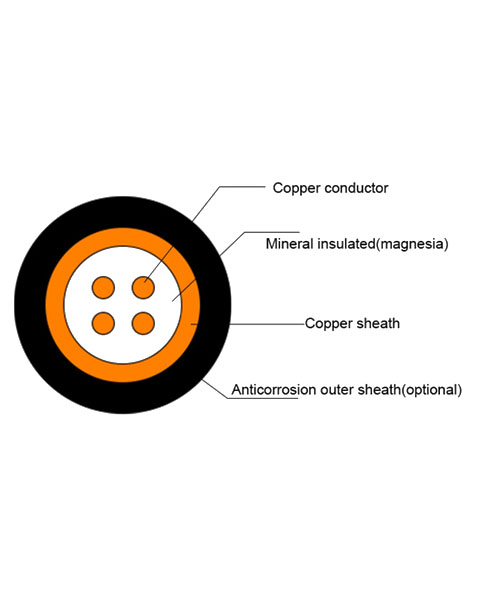
There is a similar cable with metal instead of copper jacket to wrap the core wire and insulation material, called mineral insulated metal jacket cable.
Introduction to the characteristics of it
Since the cable is composed of inorganic materials (copper and magnesium oxide powder), it will not cause a fire itself, and it is impossible to burn or ignite. Since the melting point of copper is 1083℃ and the melting point of magnesium oxide is 2800℃, this kind of cable can keep the power supply in the case of fire close to the melting point of copper.
It is a fire proof cable in the real sense. Ar hyn o bryd, it is the only safe type of electricity that can maintain power supply for three hours in a 1000℃ fire and withstand the impact of fire water spray and heavy objects falling.
Advantages of mineral insulated cable
Because all the materials of mineral insulated cable are inorganic materials, it has some advantages that other cables are impossible to have. Mineral-insulated cables are composed of copper and mineral insulating materials. They do not burn or contribute to combustion and can continue to operate in conditions close to flame. Not only that, there are many advantages of mineral cable, let’s take a look!
High operating temperature: Mineral insulated cable can withstand continuous operating temperature up to 250℃. Ac, in an emergency, the cable can be operated for a short period of time at temperatures close to the melting point of the copper sheath (which melts at 1083℃).
Long service life: The inorganic materials used in mineral insulated cables can ensure the stability, fire resistance and service life of the cables.
Explosion-proof: Highly compacted insulating material in mineral insulated cables to prevent the passage of steam, gas and flame between the equipment parts connected to the cables.
Small outside diameter: The diameter of mineral insulated cable is smaller than that of other cables with the same rated current. If the mineral insulated cable is completely submerged in water, it can continue to operate with the help of its seamless metal jacket.
High mechanical strength: Mineral insulated cables are strong and durable and can withstand severe mechanical damage without compromising their electrical properties.
Large carrying capacity: For cables of the same section, mineral insulated cables transmit higher current than other types of cables. Ar yr un pryd, mineral insulated cables can also withstand considerable overload.
Short Circuit Fault rating: Mineral insulated cables have significantly higher short circuit fault ratings than other types of cables at the same temperature.
Ground: For mineral-insulated cables, a separate ground wire is not necessary because the copper sheathing used in this cable already acts as a ground wire and provides good low ground resistance. As far as grounding sheath loop (ESR) wiring is concerned, the outer copper sheath can be used as both ground and neutral conductor in MEN (multi-ground neutral) systems.
High corrosion resistance: The copper sheath of mineral-insulated cable has high corrosion resistance, and for most installations, it does not require additional protection. Where the copper sheath of the cable is vulnerable to chemical corrosion or industrial contamination, a plastic-coated sheath should be used to protect the mineral-insulated cable.
Model
Mineral insulated cable is a special cable with special purpose, and its commonly used models are as follows:
YTTW metal-sheathed inorganic mineral insulated flexible fireproof cable
BTLY copper core isolated flexible mineral insulated fireproof cable
BBTRZ copper core non-metallic sheathed flexible mineral insulated cable
HFTGB copper core ceramic insulated metal sheathed flexible mineral insulated fireproof cable
FTGYZ copper core metal sheathed flexible fireproof cable
BTTZ copper core copper sheathed magnesia insulated heavy duty fireproof cable (rigid fireproof cable)
Ar yr un pryd, according to its different structure, mineral insulated cables are divided into light and heavy two kinds
Lightweight copper core copper sheathed mineral insulated cable:
BTTQ lightweight copper core copper sheathed mineral insulated cable;
BTTVQ lightweight copper core copper sheathed PVC sheathed mineral insulated cable;
LSF-BTTQ lightweight copper core copper sheathed low-smoke halogen-free outer sheathed mineral insulated cable;
Heavy mineral power cable:
BTTZ heavy duty copper core copper sheathed mineral insulated cable;
BTTVZ heavy duty copper core copper sheathed PVC sheathed mineral insulated cable;
LSF-BTTZ Heavy duty copper core copper sheathed low smoke halogen free outer sheathed mineral insulated cable.
Main construction methods
Construction machinery and tools:
Mineral insulated cable installation and construction machines mainly include two parts, the tools used in cable laying and cable connection and cable head making tools, cable connection and cable head making tools, including screwdriver, carp pliers, self-made peeling wrench, cutter, LPG spray gun or jet lighter,
Process flow:
Lay the cable to the corresponding distribution box according to the construction drawings, and leave enough space. When the intermediate connector is needed, lay the cable in two sections to both ends of the electrical equipment. When laying single-core cables, label the outer shell of the cables to distinguish the phase sequence when installing the distribution box.
Making the cable end: strip the cable skin → cover the terminal sleeve → screw on the brass can → roast the cable with fire to discharge the moisture in the cable → seal with hot melt glue and cover the sealing ring → Wait for the hot melt glue to cool and solidify and cover the cable end.
Making of intermediate connector: Skinning cable – set of envelope on both ends – screw on brass pot, according to the fixed connecting pipe size brass pot position to roast cable discharge cable inside the moisture, using hot melt adhesive sealing, sealing ring and wait for the hot melt adhesive on cooling solidification, the connection copper tube, heat shrinkable sleeve first set in the cable end to use magnetic column connecting cable fire, roast color are set to set connection on the copper pipe and tighten the cable.
Analysis and summary of key and difficult points
The production of the entire cable terminal and intermediate connector focuses on the sealing of the terminal end. Since the interior of mineral insulated cable is made of magnesium oxide powder as the insulating layer without the protection of PVC insulation layer, once the internal magnesium oxide powder is affected by moisture, the insulation will be seriously affected. Felly, the sealing work becomes the top priority of mineral insulated cable. Cables must be sealed during cable transportation and installation.
When making the terminal sealing end, it must be heated at high temperature to bake all the moisture at the end of the cable. The tightening distance of the sealing tank should be well controlled. The cable incision should only be one centimeter from the inner opening.
Cable terminal sealing, especially multi-core cable terminal sealing, has many production procedures. Many parts need to be first put on the cable in order, and then moved to the corresponding position to tighten and fix after the sealing tank is installed.
Every operation step must be kept in mind during production. Once a part is forgotten to be put on the cable first, the cable cannot be put into the sealed tank after production. The only way to waste the cable and the sealed tank is to cut the cable from the back end of the sealed tank and make it again. Felly, operators are required to master the operation sequence.
Difficult because of high layer building now, evacuation, fire power supply system can continue to work after requirements, ensure the normal conduct of evacuation, and so on power supply cable fire demand is higher and higher, mineral insulated cable due to its refractory, the characteristics of high temperature resistant, in high-rise buildings, especially in public buildings will be more and more widely used.
Due to the particularity of the material, the construction technology of the cable and the cable is different, according to the project construction experience, this paper simply introduces the cable head production and the production process of intermediate connector, caused by a lack of experience, also appeared in the process of construction order not to waste into cable terminal head, to share with you here, hope to get some experience and lessons, The same error will not be made in the future operation.