La ingeniería de cables submarinos es reconocida mundialmente como un proyecto técnico difícil y complejo a gran escala.
Tanto el diseño del cable, fabricación, y la construcción de tendido son mucho más altos que otros productos de cable generales.
Entre ellos, son las juntas intermedias del cable submarino, la producción de terminales, instalación, y cableado. Y la puesta en marcha de pruebas también es una parte muy importante de esta compleja ingeniería técnica.
Su producción, y la calidad de la instalación es buena o mala, y la seguridad y la fiabilidad de toda la transmisión y la subestación juegan un papel muy importante.
El cable submarino es lo que
El cable submarino se coloca en ríos, lagos, y Cable de alimentación submarino de mares, también conocido como cable submarino.
Se compara con cables terrestres, Hay poca diferencia en el aislamiento principal.
Debido a los métodos de construcción especiales y las condiciones de funcionamiento de los cables submarinos, en la armadura, chaqueta de metal, longitud de fabricación. Y otros aspectos estructurales de las diferencias más grandes.
Los cables submarinos a menudo se fabrican en grandes longitudes de cables enteros, que deben ser enrollados en círculos para el transporte.
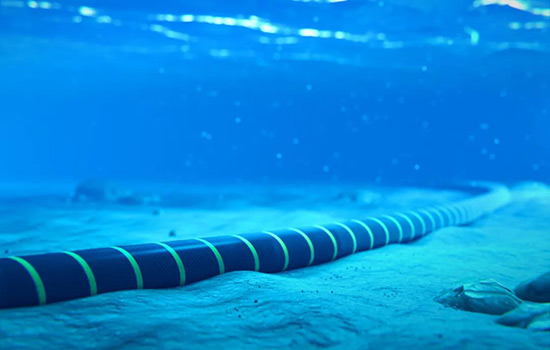
Aunque la armadura con tono corto puede reducir el diámetro de la enrollamiento. El cable submarino con armadura de lanzamiento corto es fácil de anudarse bajo el agua cuando está bajo una gran tensión en el proceso de colocación.
Por lo tanto, El tono de armadura general necesita 12-14 veces el diámetro promedio de la armadura.
Para reducir el diámetro de la enrollamiento, Algunos usan alambre de acero preestablecido de lanzamiento corto o doble armadura de alambre de acero, y algunos usan armadura con la dirección opuesta del giro interno y externo.
¿Cuáles son los tipos de cables submarinos??
En cuanto a la estructura
Principalmente dividido en cable submarino de tres núcleos y cable submarino de un solo núcleo, bajo- y líneas de voltaje medio usando un cable submarino de tres núcleos. Y líneas de alto voltaje Usando un cable submarino de un solo núcleo.
En términos de función
Hace medio siglo, El cable submarino es solo una función simple de transmisión de energía eléctrica.
Ahora el cable submarino integra dos funciones, realizando efectivamente la transmisión de energía eléctrica y señales en el mismo cable.
De la composición de aislamiento
Hay cables submarinos aislados llenos de aceite y cables submarinos aislados de plástico extruidos.
Sobre el tipo de carga
Hay cables de CC y AC.
El cable submarino de DC se caracteriza por baja pérdida, transmisión de energía a larga distancia fácil de alcanzar.
Sin embargo, la experiencia de aplicación del cable submarino de CC no es rica. Y los costos de construcción de respaldo de las estaciones convertidoras y otras son altos.
La pérdida de cable submarino de CA es grande, pero la tecnología de operación y mantenimiento está madura, Apoyando los pequeños costos de construcción.
Por lo tanto, Los diseñadores de línea de cable submarino generalmente tienen que hacer compensaciones técnicas y económicas para maximizar los beneficios.
Cómo alambre de cables submarinos
Encuesta de enrutamiento de cables submarinos
La encuesta de enrutamiento de cable antes de la colocación de cables submarinos incluye:
① Limpia la profundidad del agua, topografía, y medición de perfil estratigráfico poco profundo del área de enrutamiento en alta mar.
② Muestreo de superficie de sedimento, muestreo de columna, y encuesta de tacto estático.
③ También incluye encuestas de tráfico y condiciones de construcción y obstáculos que reflejan el estado de las actividades de desarrollo marino.
Recientemente, el uso de posicionamiento avanzado de posprocesamiento GPS y (CPT) Tecnología de tacto estático ha llevado a un aumento significativo en la velocidad y efectividad de la encuesta..
Cable submarino
El proyecto de colocación de cable submarino es reconocido como un proyecto complejo y difícil a gran escala de países de todo el mundo.
La colocación del cable debe controlar el ángulo del cable al agua y la tensión de la colocación controlando la velocidad de navegación del recipiente de colocación y la velocidad de liberación del cable para evitar dañar el cable debido a un radio de flexión demasiado pequeño o demasiada tensión.
En mares poco profundos, como la profundidad del agua de menos que 200 metros en el mar, el cable está enterrado.
en las profundidades del mar, el cable está tendido, y el cable es liberado por el recipiente de colocación de cable. Y el cable se monitorea y se ajusta constantemente utilizando monitores submarinos y vehículos de control remoto submarino.
También, Controle la velocidad y la dirección de avance del barco de colocación y la velocidad de colocar el cable para evitar dañar el cable pasando por alto lugares y rocas desiguales.
Flush Protección de entierro de cables submarinos
En la etapa final de construcción, El objetivo principal es proteger el cable submarino mediante un entierro profundo para reducir el impacto del entorno marino complejo en el cable submarino y garantizar la seguridad operativa..
En la zona arenosa y limitada, una trinchera sobre 2 Los medidores de profundidad se generan por agua de descarga de alta presión para enterrar el cable en él, y el suelo arenoso a su lado lo cubre.
Para las áreas de arrecifes de coral y arcilla, cortar una trinchera 0.6 – 1.2 metros de profundidad con un cortador, enterrar el cable en la zanja y rellenarlo naturalmente para formar protección.
En las zonas de roca dura, El cable debe cubrirse con una cubierta de cemento y otros objetos duros para implementar la protección.
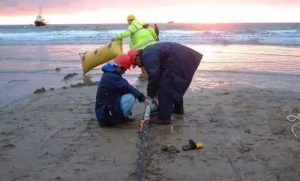
Cómo impermeabilizar la línea de cable submarino
Es un alambre envuelto con material aislante para aislar agua del cable., proporcionando así una función impermeable.
El cable se realiza de tal manera que el cable se incruste primero en un compuesto de gelatina que protege el cable del daño incluso en caso de contacto con el agua de mar.
Él cable de fibra óptica Luego se empaqueta en un tubo de acero para evitar que la presión del agua lo dañe.
próximo, Está envuelto en un alambre de acero muy fuerte en general y se rompe en un tubo de cobre., y finalmente, Se aplica una capa protectora de material de polietileno.
Cerca de la costa de la plataforma continental, Los cables submarinos generalmente se colocan con cables más ligeros con cables de acero más fuertes y se cubren con un recubrimiento de asfalto para evitar la corrosión por agua de mar.
Cable submarino cómo anticorrosión
Los cables de fibra óptica submarina son altamente susceptibles a la corrosión del agua de mar porque están sumergidos en agua de mar altamente concentrada durante largos períodos.
Además, Las moléculas de hidrógeno pueden difundirse en el material de vidrio de la fibra, Hacer la pérdida de la fibra más grande.
Por lo tanto, Los cables de fibra óptica submarina deben evitar la generación interna de hidrógeno y la infiltración de hidrógeno en el cable de fibra óptica desde el exterior.
Actualmente, Los cables de fibra óptica submarina se construyen envolviendo en espiral la fibra óptica recubierta de una vez o dos veces alrededor del centro y reforzando a los miembros a su alrededor.
Lo anterior es una introducción a los cables submarinos. Si tiene alguna pregunta sobre la compra de cable, Bienvenido al cable de Like ZMS.